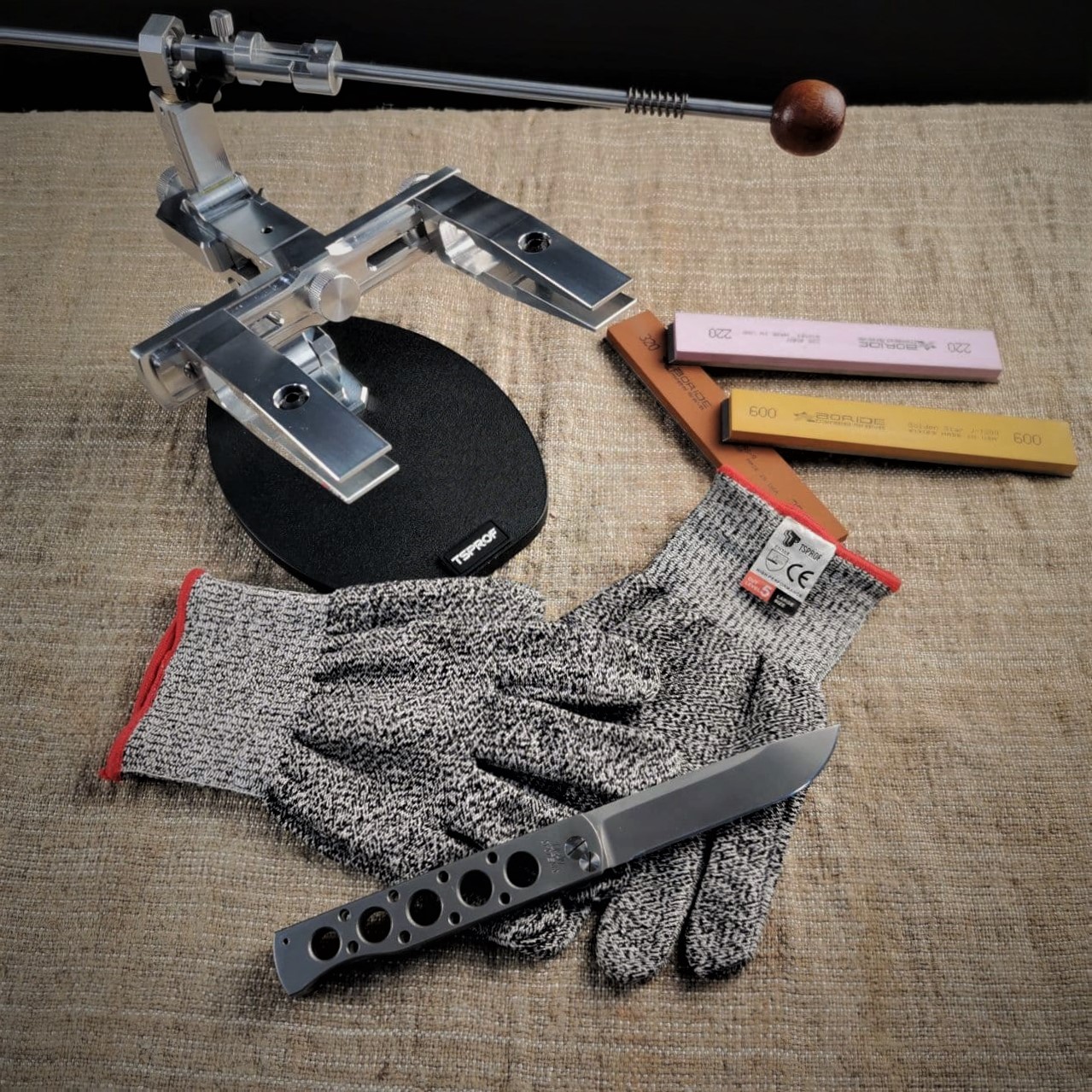
Арамидное волокно
Материал «арамид» представляет собой так называемый ароматический полиамид (aromatic polyamide) – длинную цепочку синтетического полиамида, то есть пластмассы на основе линейных синтетических молекулярных соединений, содержащих в основной цепи амидные группы −CONH−. Свойства полученных из полиамида волокон определяются одновременно химической и физической микроструктурой. Амидные связи обеспечивают высокую энергию диссоциации, то есть прочность химической связи и повышенную термостабильность. Всего известны три типа применяемых в промышленности арамидных волокон: пара-арамиды (п-арамиды), мета-арамиды (м-арамиды) и сополимеры полиамида.
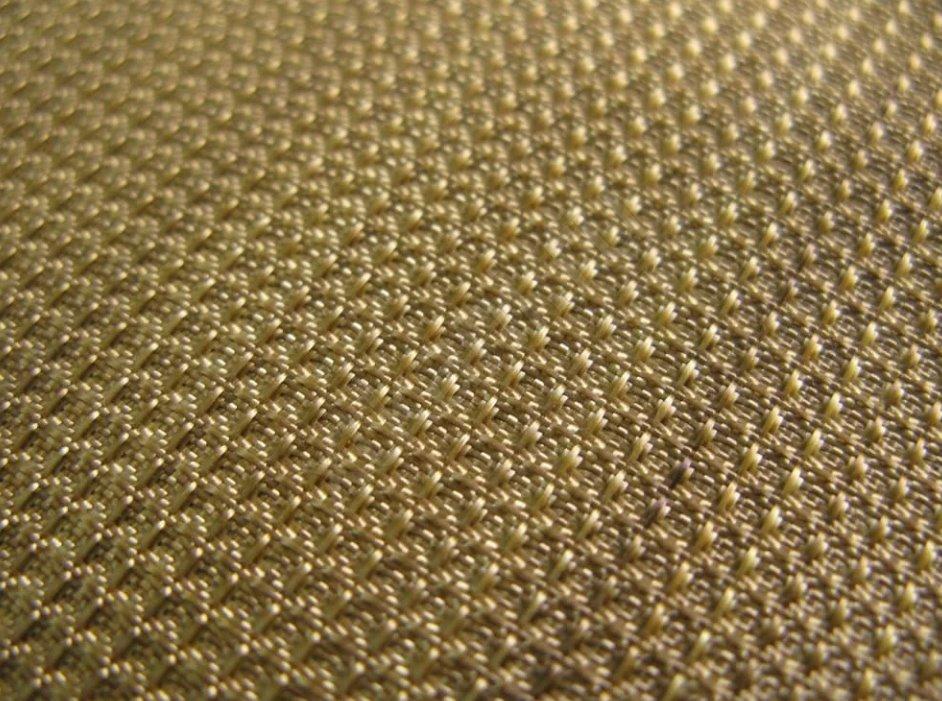
Источник фото: https://xtkani.ru/aramidnaya/
Самые известные в мире пара-арамиды производятся под торговыми марками Kevlar и Twaron. Серийно производимые волокна Kevlar 29, Kevlar 49, Kevlar имеют большой модуль упругости и для разрыва такой ткани необходимы большие усилия: от 250 до 600 кг на квадратный миллиметр. Кевлар имеет плотность 1400-1500 кг/м куб, что почти в 2 раза легче стекловолокна. Важным свойством этого материала является то, что он практически не подвержен горению и плавлению при высоких температурах. Кроме того, кевларовые волокна являются электроизолятором и упрочняются на холоде, позволяя применять изделия из ткани в самых тяжелых климатических условиях. Кевлар отличается мягкостью, гигроскопичностью и способностью к воздухообмену. Все эти свойства обуславливает применение пара-арамидов в качестве корда для шин, а также различных баллистических и композитных материалов. Высочайшая прочность позволяет противостоять пулевым ударам и применяется при изготовлении бронежилетов.
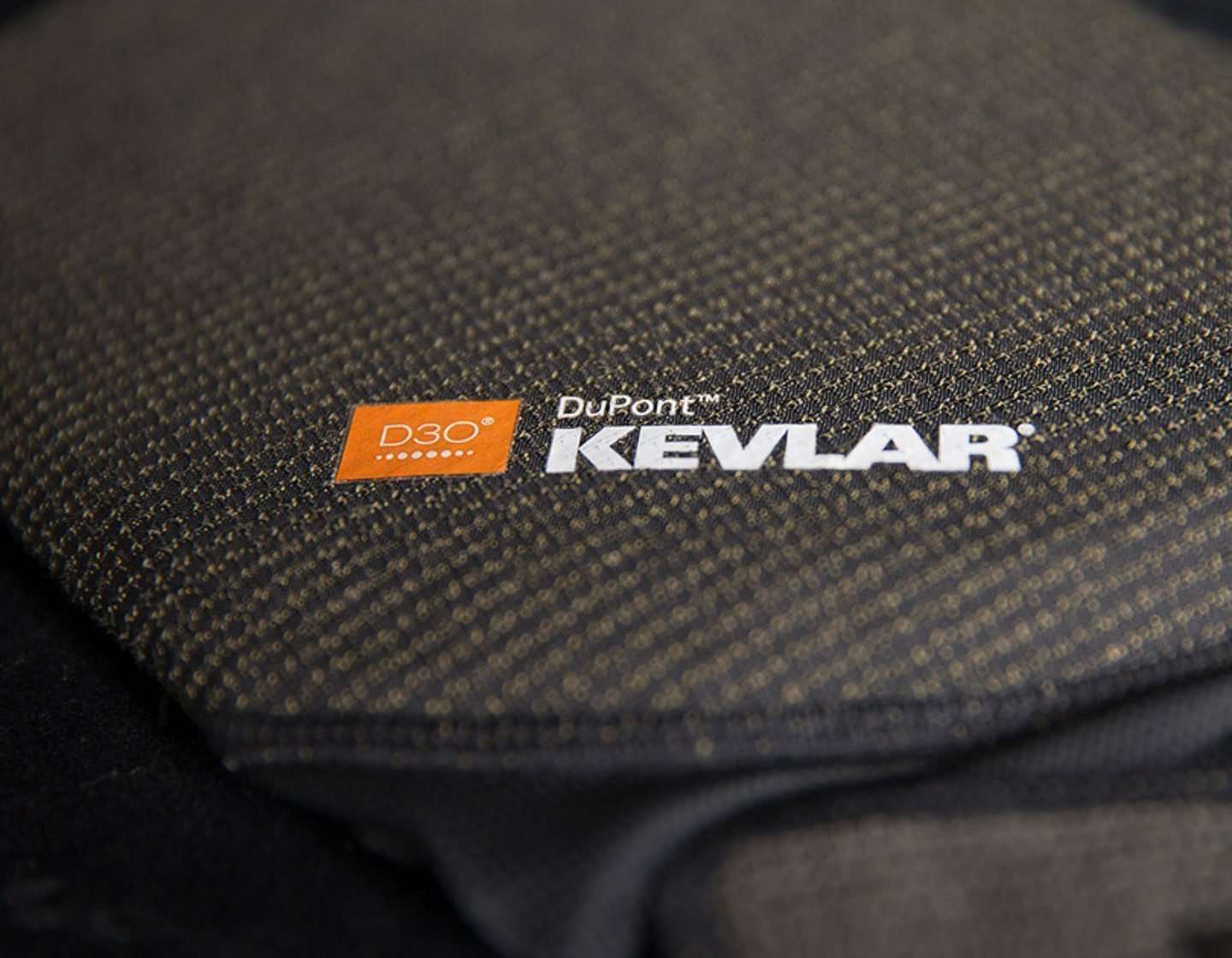
Источник фото: https://www.partner-moto.ru/blog/kevlar-material-kotoriy-zaschischaet-mototsiklistov/
При всех своих достоинствах кевлар, также имеет явные недостатки: его нельзя чистить химическими реагентами, подвергать воздействию солнечных лучей. При намокании прочность кевларового волокна уменьшается почти в 2 раза, а при высыхании не восстанавливается в полном объеме, кроме того, кевлар очень быстро стареет и утрачивает свои свойства в течение 10 лет с момента изготовления. Ну а главным недостатком этого материала является конечно же высокая цена. Поэтому перчатки, предохраняющие от порезов чаще всего, создаются не полностью из кевлара, а из ткани, армированной кевларовыми нитями. Перчатки изготовленные на основе кевлара надежно выдерживают режущий удар ножа и не тяжелый секущий удар. Но, как и другие подобные перчатки не способны противостоять колющему удару. И если толстый кевларовый бронежилет способен выдержать колющий удар ножом, то тонкая перчатка не может этого сделать.
Волокна Dyneema (СВМПЭ)
Сверхвысокомолекулярный полиэтилен (СВМПЭ, англ. Ultra-high molecular weight polyethylene, HPPE) — термопластичный полимер, конструкционный материал, применяемый для работы в экстремальных условиях эксплуатации. Молекула СВМПЭ состоит из длинных линейных цепочек полиэтилена с относительно слабыми межмолекулярными связями. Это отличает СВМПЭ, от кевлара, который обладает короткими молекулами и крепкими молекулярными связями. В Европе волокна СВМПЭ известны под маркой Dyneema, в США - Spectra.
Изделия из СВМПЭ получаются следующими методами обработки:
Прессование;
Непрерывное профильное прессование, или штранг-прессование
Гель-формирование (гель-прядение);
Плунжерная экструзия.
Именно с помощью гель-формирования получают самые прочные волокна марок Dyneema и Spectra для тросов, строп, для использования в баллистической защите, в сфере оборонных технологий.
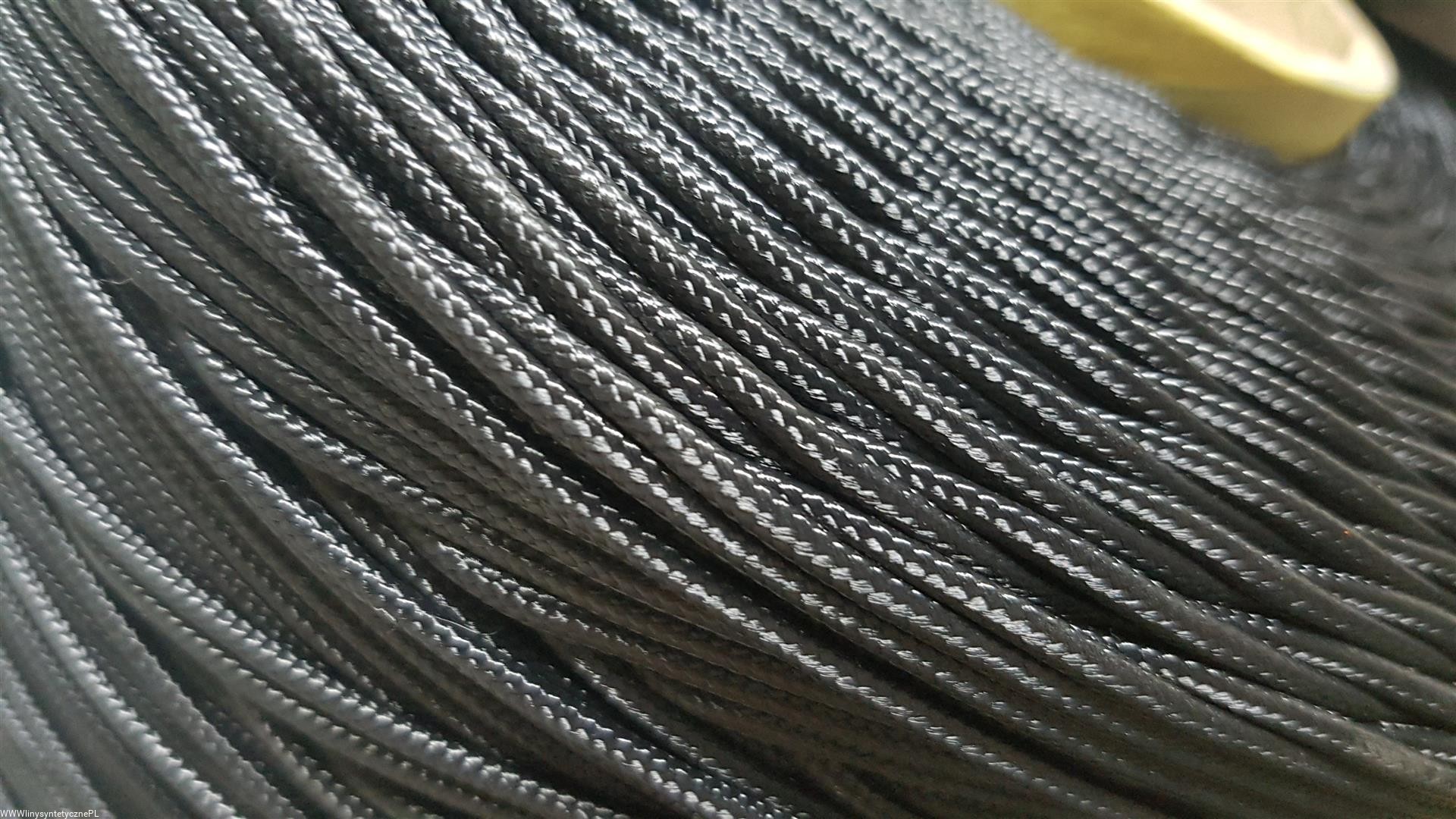
Источник фото: https://linysyntetyczne.pl/lina_dyneema_3MM_oplot_poliestrowy
В процессе производства пластичную массу СВМПЭ растворяют в декалине и затем выдавливают в водный раствор, а получившийся гель вытягивают при температуре около 100 градусов, удаляя при этом растворитель. В процессе формования, состоящие из длинных линейных цепочек полиэтилена молекулы, закручиваются в волокна, и теряют межмолекулярные связи. В результате этого процесса ориентация молекул становится параллельной, а за счет высокой молекулярной массы волокна становятся прочными, нерастяжимыми, нейтральными к водным и химическим растворам, получают высокую износостойкость, устойчивость к ультрафиолету и небольшой вес.
При сравнении волокон Dyneema с кевларом, первые выигрывают по многим характеристикам. В частности: по прочности на разрыв, по устойчивости к ультрафиолетовому излучению, а главное по стойкости к намоканию, которая существенно понижает прочностные качества кевлара и совершенно не оказывает воздействия на свойства высокомодульного полиэтиленового волокна.
Именно из материала HPPE изготавливаются перчатки TSPROF, обладающие 5 классом защиты от порезов по европейскому стандарту DIN EN 388: 2003.
Механические риски и методы их испытаний определяются в стандарте DIN EN 388: 2003 по следующим критериям:
1. Устойчивость к истиранию.
Проверяется обработкой перчатки наждачной бумагой под давлением. Число циклов необходимых для протирания отверстия в материале служит эталоном. Максимальным уровнем считается 8000 циклов.
2. Устойчивость к порезу.
Определяется с помощью вращения круглого лезвия, которое прорезает перчатку с постоянной скоростью. После чего происходит сравнение с эталонным материалом служит эталоном и результирующим индексом. Максимальный индекс 20.
3. Сопротивление разрыву.
Для проверки сопротивления на разрыв материал перчаток сначала разрезается. Сила, необходимая для разрыва материала, служит эталоном. Максимальный уровень эффективности составляет 75 ньютонов.
4. Прочность к проколу.
Для измерения сопротивления к проколу, перчатка пробивается гвоздем определённого размера. Используемая сила служит эталоном. Максимальный уровень эффективности составляет 150 ньютонов. Этот тест испытывает только прочность самой ткани, но не способность печатки защищать руку от травм. Перчатки не могут защитить от колющего удара и даже есть ткань выдержит давление, рука человека все равно будет травмирована.
Синтетические волокна, смешанные со стекловолокном и металлическими нитями
С целью усиления надежности перчаток от порезов применяется технология смешивания волокон кевлара или высокомолекулярного полиэтилена с нитями из стекловолокна и металлов. В частности, в таких перчатках может применятся основа из 55% HPPE (молекулярный полиэтилен), 20% нейлона, 15% стекловолокна, 10% спандекса, с покрытием – 100% полиуретана. Перчатки могут быть выполнены в технике платированного вязания – гладкая нить HPPE размещается на внутренней, соприкасающейся с кожей стороне перчатки, что придает дополнительный комфорт при работе. Покрытие ладони и кончиков пальцев из 100% полиуретана улучшает захват и увеличивает срок эксплуатации перчаток. Тыльная сторона перчаток зачастую остается без покрытия, что позволяет коже дышать.
Другой технологией является вшивание в ткань металлических нитей. На основу из высокомолекулярного полиэтиленового волокна HPPE добавляются волокна нержавеющей стали, стекловолокна, полиэфирных и полиамидных волокон. Такие перчатки изготавливаются бесшовным способом и обеспечивают комфортную носку и подвижность руки.
Перчатки от порезов безусловно необходимы всем, кто в течение длительного времени работает с острыми предметами и, в частности, точит ножи. Порезы всегда преследуют заточника и важным элементом безопасности выступают такие перчатки.