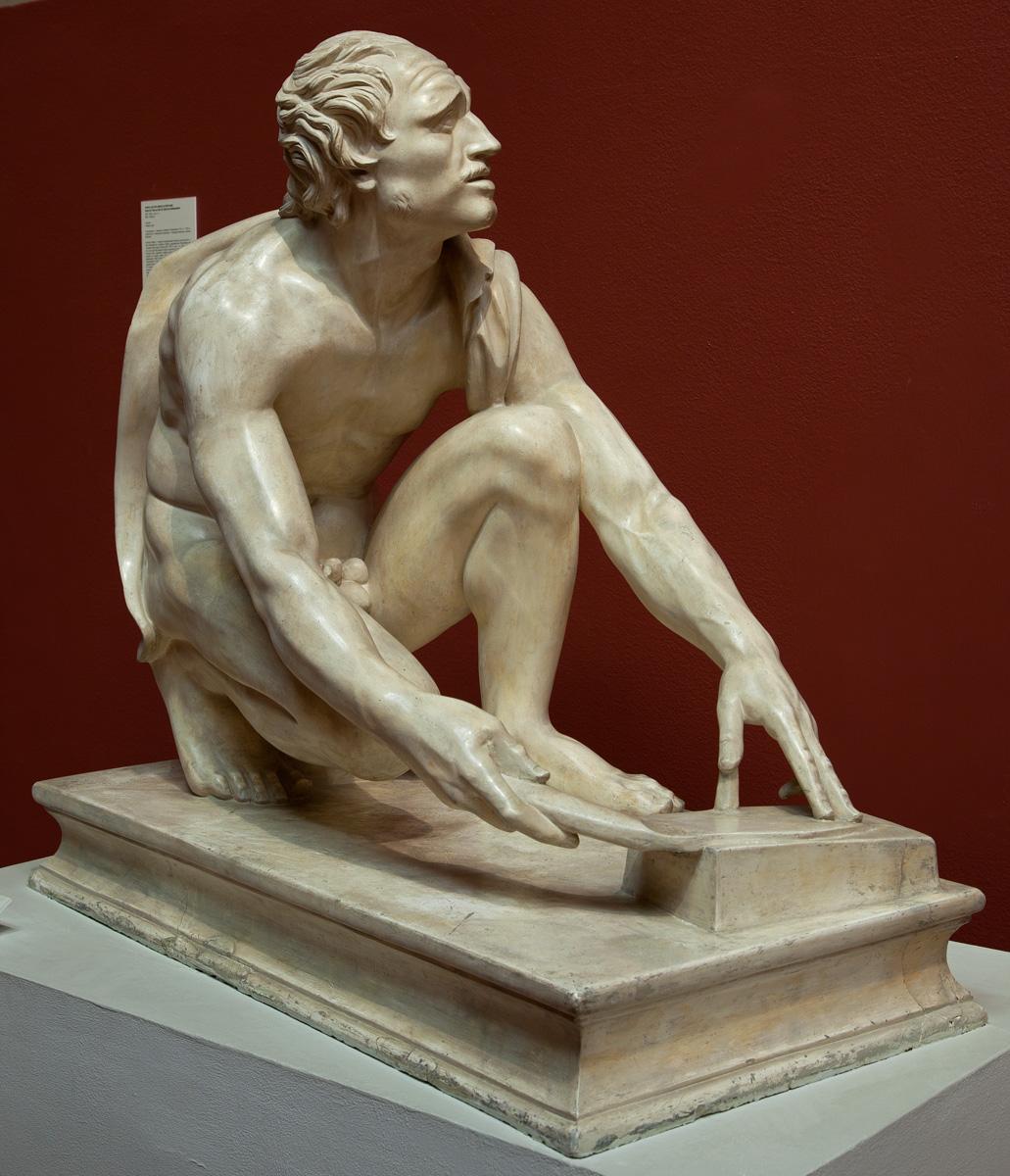
"Точильщик". Римская скульптура III - II вв.д.н.э.
Очевидно, что в течении многих столетий сам процесс ручной заточки не менялся. Мастер-заточник брал специально выравненный камень, прижимал к нему сверху затачиваемый инструмент (нож, долото, стамеску, ножницы и т.п) и с помощью смазывающей жидкости: воды или масла производил заточку. Если затачиваемый предмет был большого размера или сложной геометрии (меч, сабля, коса и т.п.), он фиксировался максимально прочно и в ход уже шли небольшие камни, которыми протачивалась режущая кромка. Главной проблемой при такой работе было удержание угла. Причем эта проблема была характерна как для ручной заточки, так и для заточки с помощью специальных заточных станков (см. статью). Постоянный угол выдерживался вручную и на точильном камне, и на вращающемся круге. Качественно такую работу мог выполнить только заточник высочайшего класса, а таких специалистов естественно было крайне мало.
Впрочем, все железные изделия изготавливались тогда из мягкой углеродистой стали, которая применялась вплоть до начала 20-х годов XX века. Они достаточно легко принимали заточку и быстро тупились, само понятие остроты носило крайне относительный характер. Однако возрастание твёрдости и переход на качественные нержавеющие стали существенно изменил ситуацию. Потребовался уже иной уровень качества заточки и в промышленных масштабах он был достигнут за счет применения электрических заточных устройств. Однако приспособления для заточки ножей и инструмента вручную не отошли в прошлое под давлением электрических точилок. Они стали атрибутом домашней заточки и максимально точной профессиональной заточки, применяемой для самых твердых премиальных сталей и дорогих художественно оформленных ножей. При этом способы удержания угла со временем менялись.
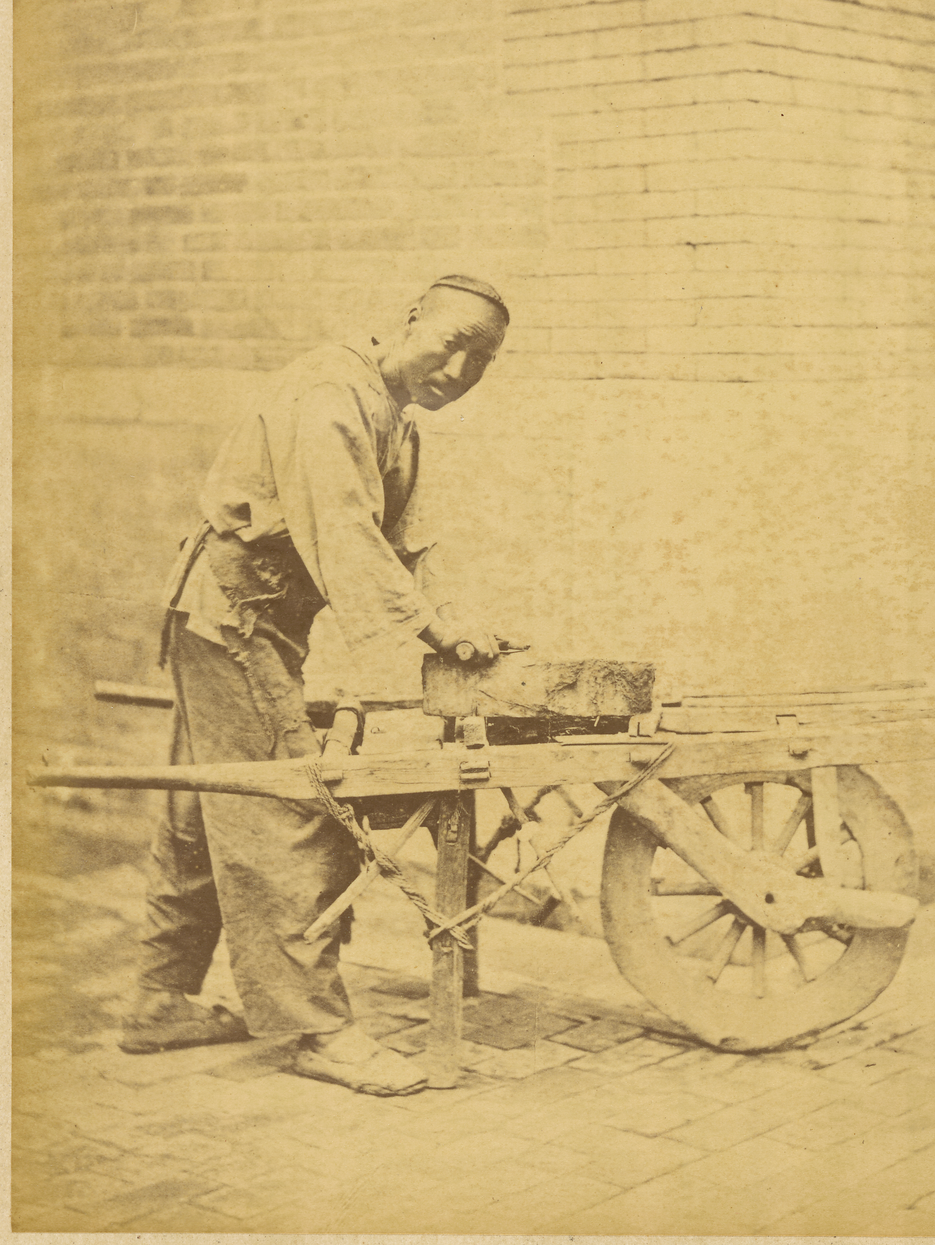
Китайский точильщик ножей 1874 год.
Простейшим способом удержания угла при заточке стало создание специальной направляющей (на сленге называемой "костылем"). Она представляет собой металлический стержень с надетыми него губками в которых фиксируется нож. За счет движения губок по стержню выставлялся угол заточки, для заточки другой стороны подвода необходимо также перевернуть всю конструкцию с зажатым ножом. Главными недостатками этого приспособления является невозможность точного выставления угла на этом устройстве, так как использовать электронной угломер затруднительно при такой конструкции, она позволит выставить угол только с достаточно большой погрешностью. Также необходимо понимать, что усилие, прикладываемое заточником к направляющей, не может быть одинаковым в течение всей работы.
Более того, усилие должно равномерно распределяться по всей длине ножа, а в случае, если нож имеет длинный клинок, его придется дотачивать по частям, так как не хватит длины поверхности камня. И в целом для работы таким устройством нужно иметь высокую чувствительность рук и особо важно иметь ее при финишной заточке и полировке клинка. Ведь с каждым следующим более тонким камнем необходимо снижать давление и к моменту полировки оно должно быть минимальным. Кроме того, ступенчатая заточка или создание микроподвода оставались исключительно сложным занятием. Заточка выпуклой линзы (конвекса) с помощью такой направляющей не представлялась возможной.
В последствии конструкция направляющей была несколько изменена и приобрела дополнительные элементы в виде специальных валиков. Они позволяли уже не водить направляющую руками, а катать ее по камню. Такое приспособление стало называться кареткой и использовалось в первую очередь для заточки столярного инструмента: ножей рубанка, стамесок и долот. Здесь также возникала проблема невозможности затачивать длинные предметы. А при заточке коротких металлических поверхностей происходил неравномерный износ камня. И если для инструмента такой метод работы на недорогих абразивах был возможен, то для ножей каретки не годились. Необходимо было искать другое решение. И со временем оно было найдено.
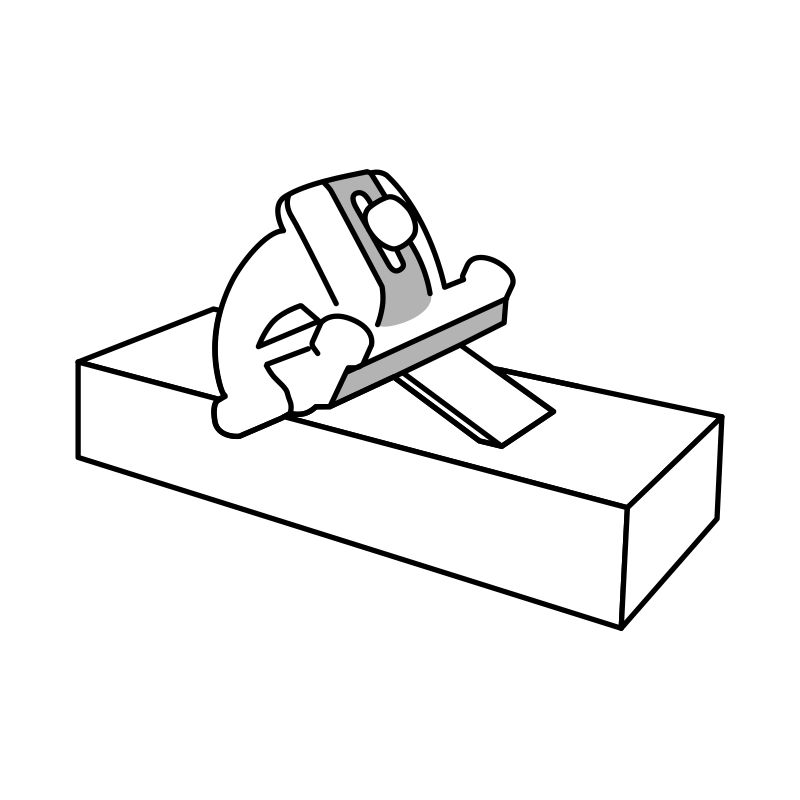
Таким решением стало создание держателя абразива на длинной металлической штанге. При его использовании уже не человек водил ножом по камню, а камень двигался сверху по поверхности подвода ножа. Первоначально такая точилка удерживалась одной рукой, а другой происходила заточка. Размер ножа, доступный для заточки сразу увеличивался, появилась возможность для заточки длинных клинков. Однако такой формат требовал больших физических усилий в случае заточки твердой стали и длительной работы. Разнообразие углов в такой точилке было ограничено небольшим количеством отверстий, в которые фиксировались направляющая. А ступенчатая заточка и создание микроподвода из-за этого становились невозможными. Заточка в линзу была в принципе возможна, но неудобна из-за технических характеристик точилки.
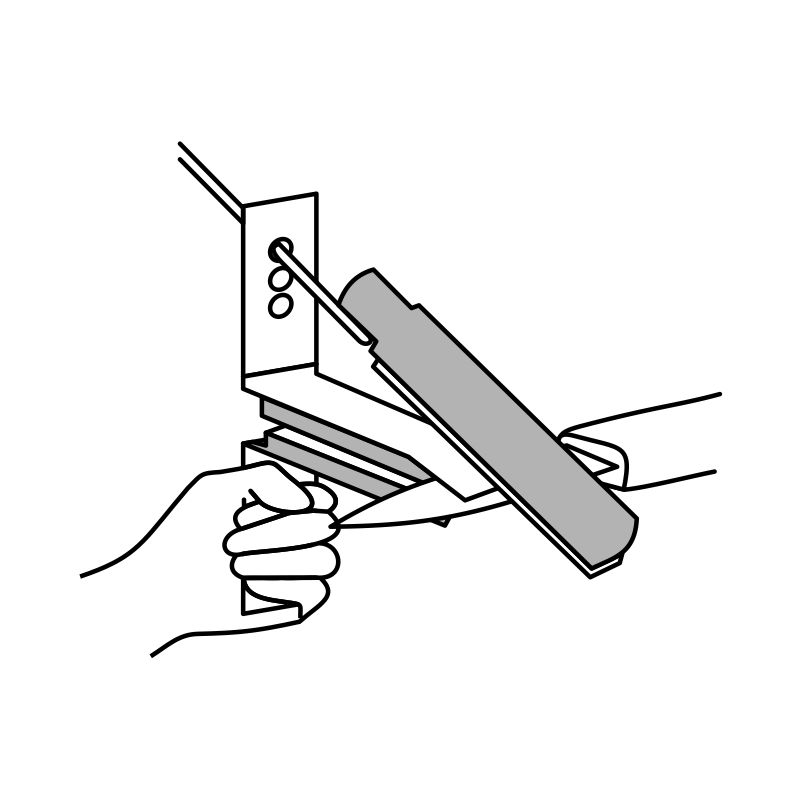
Для того, чтобы сделать работу заточника удобнее, была разработана заточная система, включавшая в себя площадку для размещения ножа и специальный подъемник позволяющий регулировать установку угла. Это решение позволило повысить точность регулировки угла и полноценно использовать при заточке электронный угломер. Теперь заточник мог работать со ступенчатой заточкой и легко делать микроподвод. Кроме того, существенно увеличился контроль над давлением на абразив. Появилась возможность для комфортной и легкой полировки клинка с помощью специальных полировальных паст и природных камней. Но при этом для переворота ножа и проточки другой стороны подвода его по-прежнему нужно было поднять с площадки или достать из зажима. Тем самым после переворота положение ножа менялось, что отражалось на точности попадания в угол. Решением проблемы стало создание поворотного механизма.
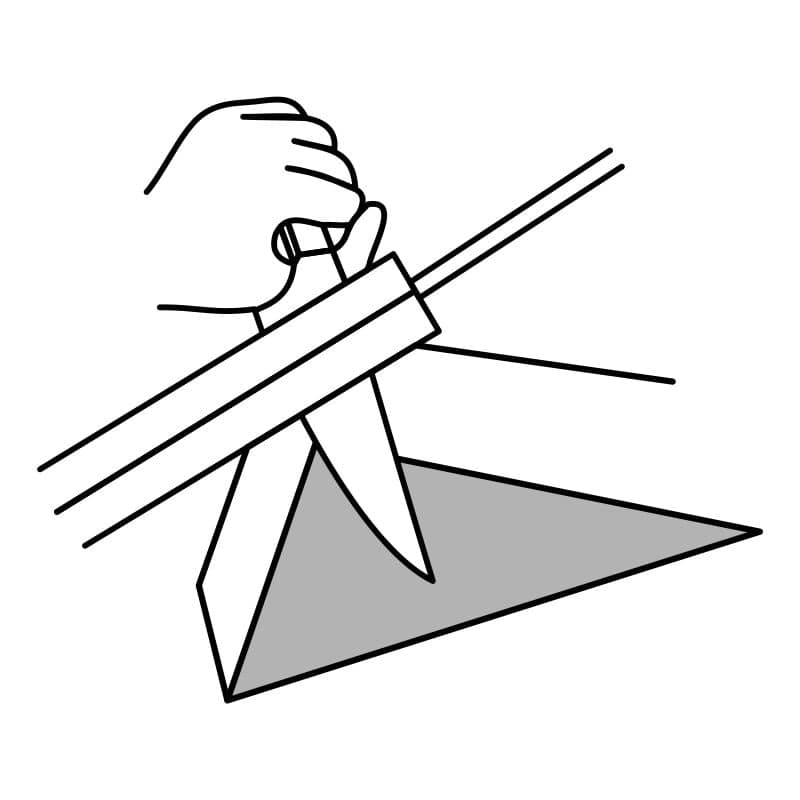
Поворотный механизм точилок TSPROF представляет собой сложную механическую систему позволяющую надежно фиксировать нож, выставлять угол для заточки с максимально допустимой погрешностью в 0,2 градуса и соблюдать симметричность при заточке обоих сторон режущей кромки ножа. Поворотный механизм может фиксироваться колесом натяжения или специальным рычагом, что придает точилке жесткость, предотвращая от появления люфтов. В то же время нож можно легко и быстро переворачивать, сохраняя угол.
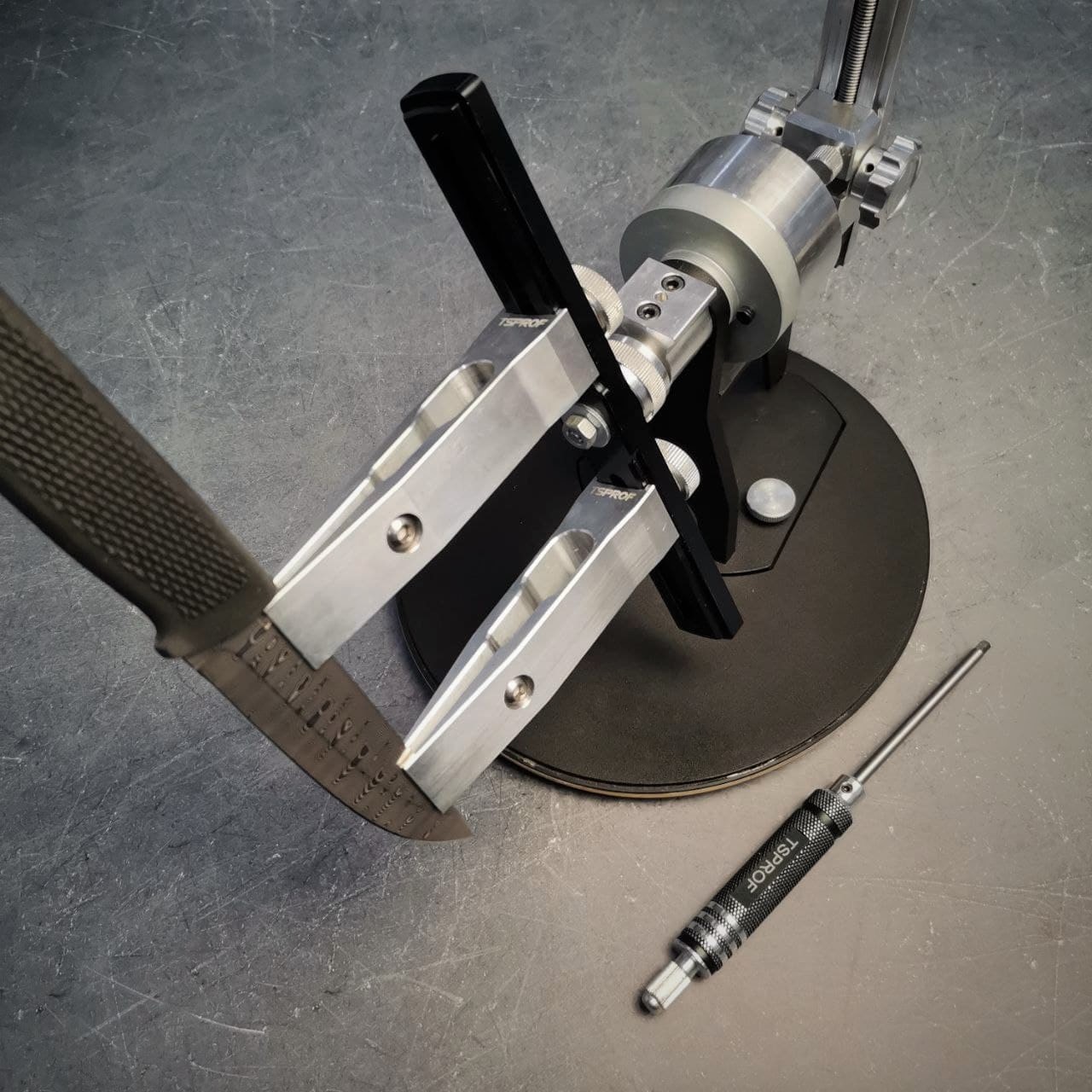
А за точность выставления угла отвечает специальный подъемник, выполненный как в виде реечного подъемника (на точилке Профиль К03), так и подъемника системы V.C. Angleset (на точилке Blitz) или дуговой стойки (на точилке TSPROF Kadet). Таким образом поворотный механизм, совмещенный с реечным подъемником, позволили решить многие проблемы заточки, которые были в прошлом. Угол заточки остается одинаковым при перевороте, возможна заточка в линзу, а также создание микроподвода и ступенчатая заточка. Современные точилки делают заточку приятным и достаточно комфортным занятием, а рутинную работу превращают в увлекательное хобби.
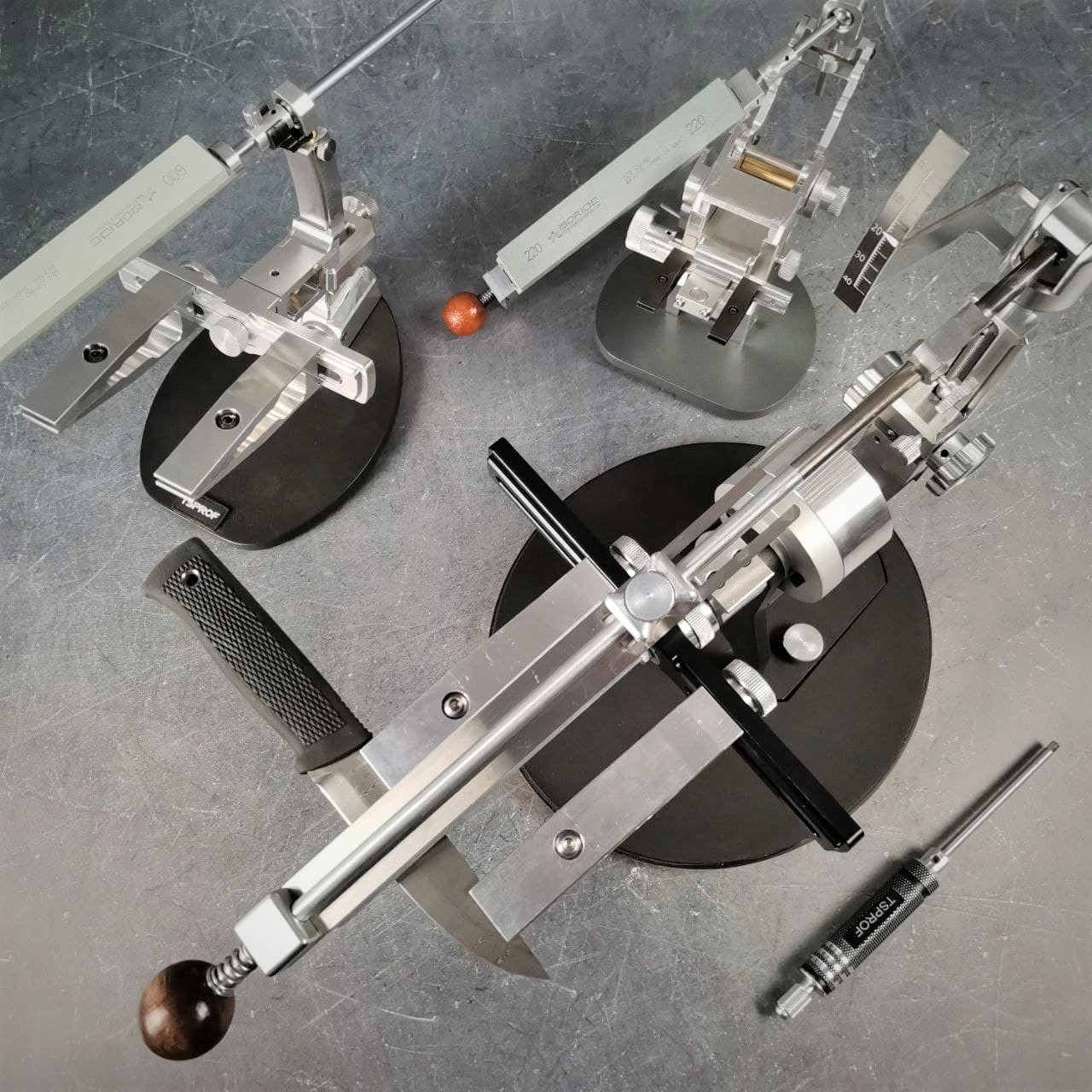
Читайте также:
История развития заточных устройств