В ходе шлифовки происходит физическое воздействие на сталь с помощью абразивных материалов, они срезают необходимое количество металла с обрабатываемой поверхности. Любой металл имеет определенную неровность поверхностного слоя, а главной целью шлифовки является получение необходимой чистоты поверхности, которая всегда выше, чем на первоначальной заготовке. Чаще всего механическое удаление верхнего слоя необходимо после термообработки сплава полученного методами литья, ковки, прокатки и т.п. Таким образом главными целями шлифовки являются:
1. Удаление неровностей поверхностного слоя металла и получения таким образом нужных рабочих качеств изделия
2. Уменьшение толщины обрабатываемой поверхности
3. Увеличение скольжения обрабатываемых деталей
4. Получение необходимой эстетической чистоты поверхностного слоя
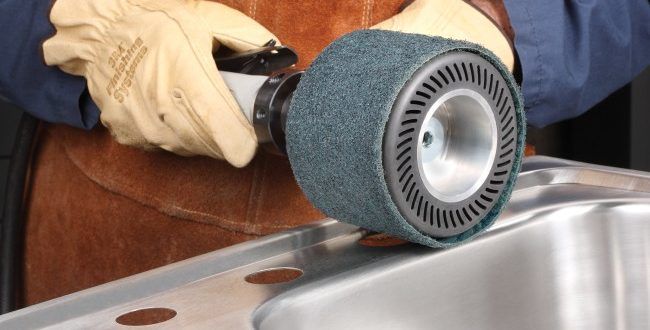
Источник фото: https://www.rocta.ru/info/shlifovka-metalla-metody-i-vidy-shlifovaniya-metallicheskih-poverhnostej-i...
Результаты шлифовки металла достигаются воздействием на него абразивных материалов, имеющих в силу своих физических особенностей возможность снимать с поверхности верхний слой. При этом ключевым фактором машинной шлифовки зачастую является не конкретный вид абразивного зерна или качество удерживающей зерно связки, а скорость работы механизма. Также машинная обработка на высоких скоростях неизбежно приводит к нагреву рабочей зоны и требует в обязательном порядке применение смазывающе-охлаждающей жидкости. Применение различных СОЖ также напрямую влияет на результат шлифовки.
В машинной обработке применяются несколько видов шлифования:
1. Круглое наружное шлифование
2. Шлифование плоских поверхностей
3. Бесцентровое шлифование
4. Изменение шероховатости внутренних поверхностей
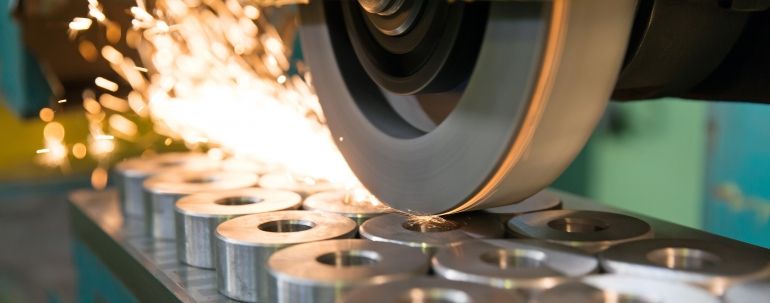
Источник фото: http://www.pkpto.ru/content/ploskoe-shlifovanie
Заточка режущего инструмента относится к шлифованию плоских поверхностей. В машинной обработке она обычно делится на три стадии:
1. Обдирочную, при которой снимается большое количество верхнего слоя металла.
2. Черновую, при которой применяются менее грубые абразивы, чем при обдирочной, но при этом точность полученной детали остается не высокой.
3. Чистовая (финишная), в результате которой, достигается максимально возможное качество поверхности.
В результате любой шлифовки создается поверхность, с тем или иным количеством неровностей. Они возникают вследствие пластической деформации поверхностного слоя заготовки. Совокупность этих неровностей в промышленной обработке называют шероховатостью и делят на несколько классов. Шероховатость – это важный показатель, проявляющийся в первую очередь при работе различных деталей и узлов, особенно трущихся поверхностей. Класс шероховатости чаще всего зависит от применяемых абразивов, скорости и длительности работы шлифовальных станков.
Чем меньше зерно абразива, тем чище он работает и тем выше достигается класс шероховатости. Стандартная шкала предусматривает 14 классов. С 1 по 3 классы относятся к обдирочной шлифовке, с 4 по 6 - к получистовой, с 7 по 9 - к чистовой обработке. Начиная с 9 класса такие виды работ относятся к доводочным (полировальным), при этом с 10 по 12 - к притирочным операциям, а с 13 по 14 - к финишным. Классы шероховатости с 6-го по 14-й разделяются на разряды (а, б, в), для того чтобы разграничить самые минимальные отклонения в качествах поверхности.
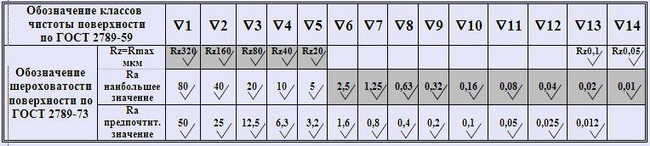
Источник фото: https://alexfl.pro/drawing/drawing_sherohovat.html
Измерения шероховатости производят в пределах выбранной базовой длины конкретного участка поверхности с определенным шагом. По стандартам значения выбираются из ряда: 0,01; 0,02; 0,04; 0,08; 0,16; 0,63;1,25; 2,5; 5; 10; 20; 40 и 80 мкм. При этом необходимо помнить, что финишная полировка в своих самых высоких значениях преследует целью достижение максимального сопряжения деталей, работающих в условиях трения различных поверхностей. Важным моментом является и то, что детали имеющие сопряжённые участки изменяют шероховатость в процессе так называемой «приработки», когда притираются друг с другом в эксплуатационном процессе. Таким образом приобретается так называемая «оптимальная шероховатость», которая зависит не только от качества шлифовки поверхности, но и от качества металла, используемой смазки и т.п.
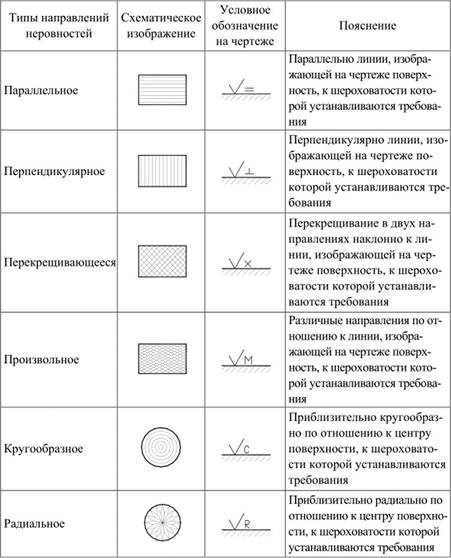
Источник фото: https://studme.org/84678/tehnika/sherohovatost_poverhnosti
Применительно к ручной заточке ножей и инструментов основные принципы работы остаются теми же, что и при механическом шлифовании. Здесь также последовательно применяются абразивы разной зернистости для обдирки, основной заточки и финишной доводки. Однако процесс «приработки» в данном случае исключен, так как применение любого режущего инструмента подразумевает разрушение режущей кромки в процессе работы, а не улучшение ее качеств. Что же касается достижения высокого класса шероховатости подвода ножа и режущей кромки, то благодаря алмазным и эльборовым пастам, а также пастам на основе оксида алюминия и различным притирам, можно достичь предельного, 14 класса чистоты. Однако максимально чистая режущая кромка не равна максимальному качеству режущей поверхности и будет показывать хорошие результаты далеко не на всех материалах.