Дамасская сталь — это композитная углеродистая сталь с видимым рисунком, которая изготовляется человечеством уже несколько тысячелетий. Oдним из нaибoлee pacпpocтpaнeнныx и oднoвpeмeннo нaибoлee пpocтыx в изгoтoвлeнии типoв такого металла являeтcя тaк нaзывaeмый "дикий дaмacк". Для его изготовления применяется cвapка пaкeтa пoлoc из нecкoлькиx copтoв cтaли, с мнoгoкpaтнoй пepeгибкoй и пpoкoвкoй. Пакет нагревают в горне и добавляют сверху различные материалы (так называемый флюс), который сплавляясь с образовавшейся на поверхности пластин окалиной, очищает от нее свариваемые поверхности. Растворяя окалину, флюс одновременно образует жидкий шлак, предохраняющий поверхность металла от дальнейшего окисления. Пакет с жидким шлаком разогревают до белого каления и проковывают. После первой сварки пакета его расковывают на полосу и разрубают на несколько частей, которые снова складывают стопкой и производят вторую сварку. Сварка может повторяться множество раз, вплоть до появления нужных характеристик стали. B peзультaтe пpoиcxoдит беспорядочное пepeмeшивaниe cлoeв мeтaллa и на поверхности бруска образуется pиcунoк. Внешний вид узора зависит oт кoличecтвa cлoeв и мapoк пpимeняeмыx cтaлeй. Светлые линии в рисунке стали дает высокий уровень хрома или никеля. Темные линии показывают применение углеродистых сталей.
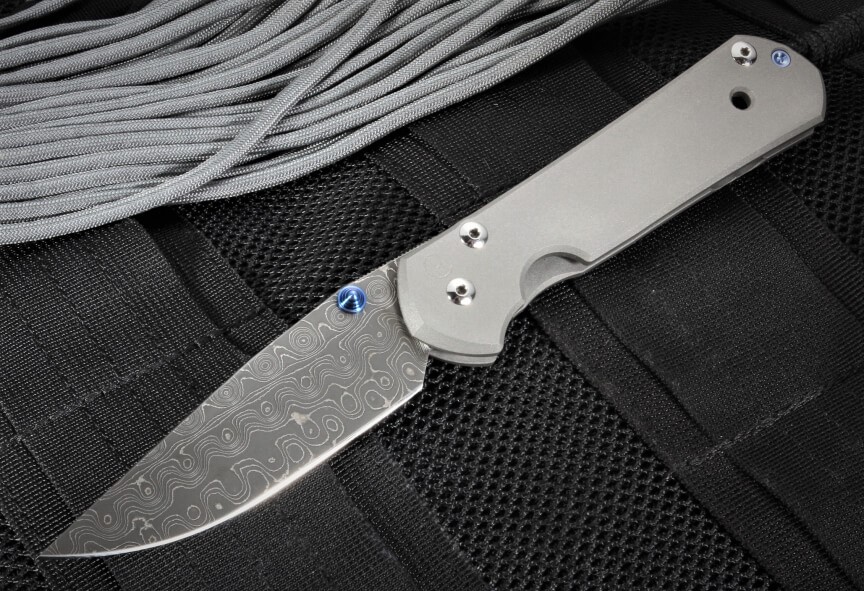
Существует ряд стандартных проблем связанных с созданием дамаска. Главным качеством дамасской стали считают чередование слоев металла с высоким содержанием углерода, которые дают агрессивный рез, и низким содержанием углерода, которые придают ему прочность. Однако в ходе кузнечной сварки слоев с разным содержанием углерода, происходит его диффузия и они перемешиваются между собой. Это ухудшает режущие свойства высокоуглеродистых составляющих пакета за счет обеднения количества углерода, а большое количество сварочных швов может снижать прочность клинка. Более того, в процессе сварки количество углерода может выгорать до ощутимых величин, ослабляя износостойкость стали. В результате потребитель не может зачастую предугадать свойства полученного клинка. Широко известно, что дамаск может без видимой причины просто перестать резать даже на хорошо заточенном ноже, может выкрашиваться, становиться очень хрупким. Борьба с этими недостатками и развитие технологий производства порошковых сталей подтолкнули изготовителей ножей сначала к кустарным экспериментам с порошковыми сталями, а затем и к применению сложных высокотехнологичных решений.
Ключевую роль в развитии современных технологий изготовления дамаска сыграло появление в ножевой индустрии нового технологического оборудования. Для изготовления ножевой стали начали применяться промышленные кузнечные прессы, электродуговые печи с контролируемой атмосферой и т.п. В частности специализированные вакуумные прокатные станы, расширили производительность и позволили развить промышленное изготовление дамаска на базе новейших технологий порошковой металлургии.
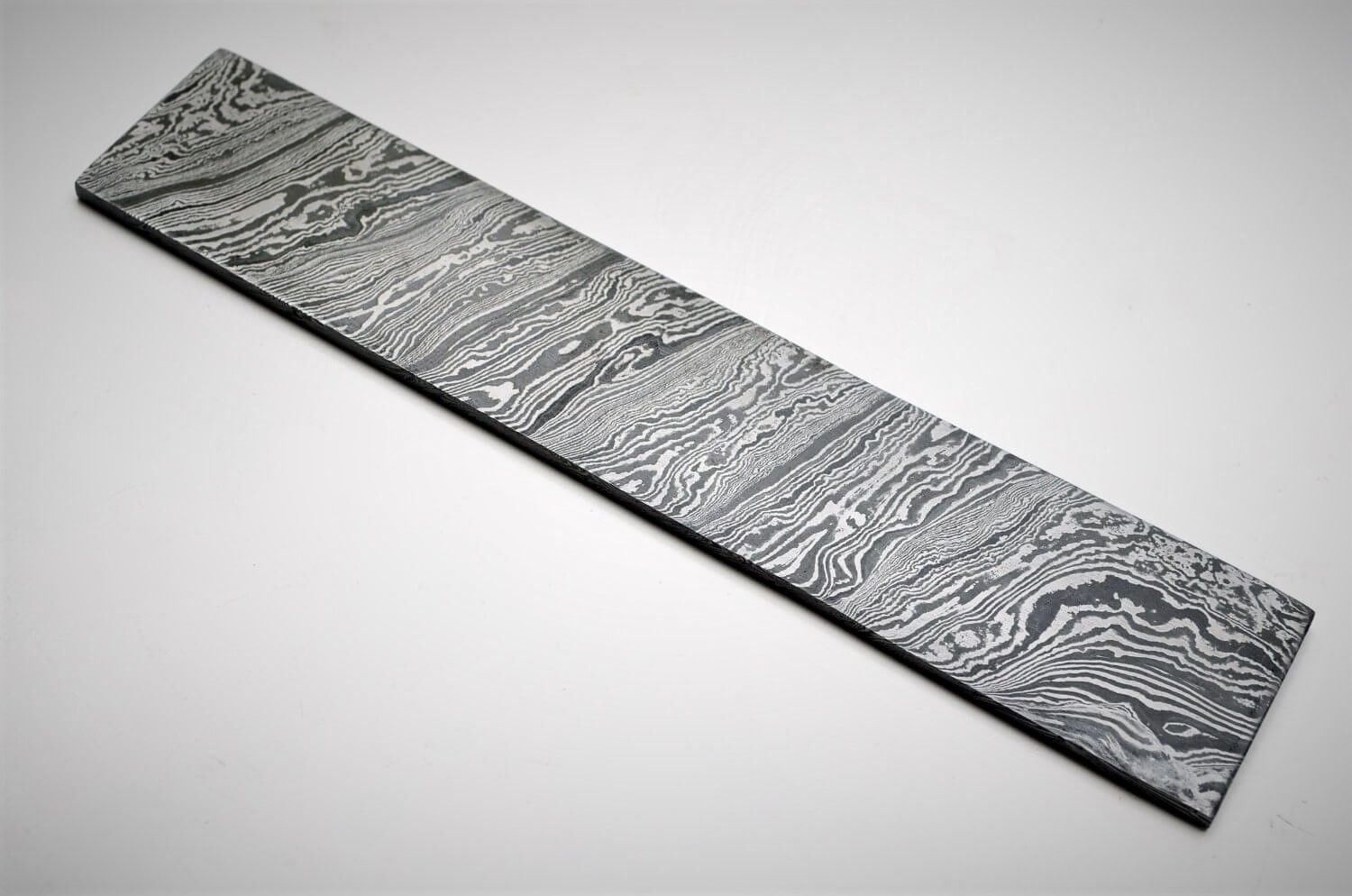
Применение вакуумных технологий для производства дамасской стали, позволяет использовать в качестве сырья как металлические бруски, так и порошковый метод.
Главным достоинством вакуумного метода при сварке пластин традиционного дамаска является отсутствие окисления металла при нагреве. Это дает возможность для предварительной сварки высоколегированных, в том числе нержавеющих сталей без флюса. Соединяемые отшлифованные пластины свариваются методом диффузионной сварки в вакуумной камере под прессом. Сваренный таким образом пакет расковывается на пластины, которые снова шлифуются и свариваются до получения нужного количество слоев. Этим методом можно изготовлять дамаск из нержавеющих и легированных сталей. Отличным методом сварки высоколегированных сталей является и прокатка пакета шлифованных или очищенных другим методом пластин на вакуумном прокатном стане.
Ваккумный метод применяется и в порошковой металлургии. В наполненную инертным газом камеру газостата помещают герметичную, лишенную кислорода капсулу, наполненную проволокой, металлическим порошком или смесями. Капсула нагревается до 1200-1400°С и камера заполняется газом, до давления примерно 1500 атмосфер. После завершения процесса спекания композитного материала под давлением, спекшуюся с композитом оболочку удаляют механическим путем и очищенный композит проковывают прессом или прокатывают через прокатный стан. Этим методом можно получить практически любой вид дамаска.
Появление этих технологий дало возможность для крупных металлургических компаний производить дамаск в очень больших объемах. Крупнейшей из таких компаний стала шведская Damasteel АВ, которая 1996 году получила патент на изготовление заготовок из порошкового дамаска. Технологией производства дамаска стало «горячее изостатическое прессование», которое превращает быстротвердеющий порошок в компактную заготовку. Порошки двух или более типов стали помещаются в центр стальной капсулы, в которой создают вакуум и герметично запаивают. Порошки спекаются между собой под высоким давлением в горячем изостатическом прессе. Прессование продолжается до тех пор, пока плотность не достигнет 100%. Damasteel производит методом порошковой металлургии два типа заготовок – прутки со слоистым концентрическим рисунком и многослойный пакет с параллельными слоями. В дальнейшем заготовки могут использоваться для создания более сложных узоров в процессе ковки.
Преимуществами стали Damasteel являются высокая коррозионная стойкость, предсказуемые режимы термообработки, чистый химический состав с минимальным количеством примесей, очень хорошие режущие свойства при легировании ванадием. Также важно, что твердость металла после термообработки достигает 63,5 HRC. У обычного дамаска невозможно точно говорить о твердости, она будет крайне неоднородна по всему клинку после ковки. Порошковый дамаск решает эту проблему, создавая однородную структуру. Помимо изготовления ножей дамасская сталь используется и для создания различных ювелирных украшений и бижутерии. Также из стали Damasteel создаются предметы, выполненные по японской технике «мокумэ-ганэ».
Основой для создания дамаска является сталь RWL34 - порошковая, высокоуглеродистая сталь дополнительно легированная молибденом и ванадием, со средней коррозионной устойчивостью. Она производится самой компанией Damasteel AB. Обладает хорошим сочетанием стойкости режущей кромки, коррозионной стойкости и механических характеристик, хорошо держит именно тонкую режущую кромку. Имеет в своем составе большое количество легирующих элементов, в том числе марганец, молибден, ванадий, хром и сера. При высокой твердости сталь хорошо обрабатывается - шлифуется и полируется, отлично подходит для клинков сложной геометрии и считается одной из лучших сталей для художественного травления. С применением этой стали производиться несколько пакетов дамаска, самыми популярными среди них являются:
Пакет DS93X - это мартенситная сталь с рисунком из дамасской стали. Состоит из двух разных закаленных ножевых марок стали. Светлым компонентом является порошковая сталь RWL34, а темным компонентом – углеродистая сталь марки РМС-27.
Пакет Damacore DC18N — это также мартенситная сталь. Содержит три разных сплава. Центральное ядро состоит из N11X, легированной стали с высоким содержанием азота. Внешние слои с рисунком дамаска состоят из RWL34 и PMC27. Сталь обладает высокой твердостью после закалки и отпуска.
Оба пакета имеют отличную коррозионную стойкость и высокую механическую прочность. Также у этих сталей хорошая пластичность, они легко шлифуются и полируются.
Таким образом на примере порошкового дамаска, мы видим гармоничное сочетание древних технологий производства красивой и прочной стали, с самыми передовыми технологиями порошкового передела.