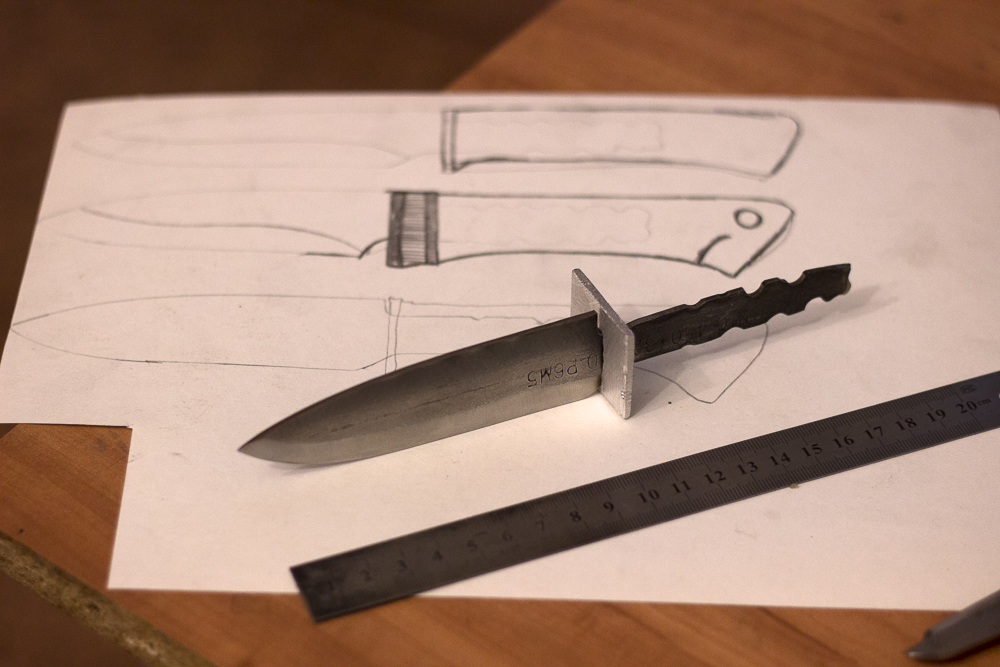
Источник фото: https://ru-knife.livejournal.com/3109608.html
Эпоха создания быстрорежущих сталей началась в XIX веке и была связана с активным развитием технологий создания изделий из металла. Существовавшие тогда резцы не справлялись с их обработкой, слишком быстро разогреваясь и изнашиваясь на больших оборотах новых станков. В 1868 году, английский металлург Роберт Форестер Мюшет, управлявший на тот момент металлургической компанией Darkhill, в ходе тысяч изнурительных экспериментов сумел создать первые образцы новой инструментальной стали. Она получила название «Специальная сталь Р. Мюшета – RMS (Robert Mushet's Special Steel)».
RMS еще не была полноценной быстрорежущей сталью. Основными легирующими элементами в ее составе были: вольфрам - в пределах 9%, марганец - 2,5%, а количество углерода составляло 1,85%. Сталь проходила после ковки термообработку воздушной струей, в то время как сплавы предыдущего поколения закаливалсь с водой. Почти 30 лет "сталь Мюшета" использовалась в станочной обработке, позволяя увеличивать скорость производства продукции и достойно справляясь с твердыми сплавами, пока на рынке не появилась первая по-настоящему "быстрорежущая сталь" американских инженеров Тэйлора и Уатта. Изготолвенные из нее резцы допускали скорость резания металла до 18 м/мин (метров в минуту). Она стала прообразом современной марки Р18 и содержала 0,8 % углерода и 17-18 % вольфрама. Р18 считалась «золотым стандартом» быстрореза на долгий период, вплоть до 70-х годов прошлого века. Затем, в связи с дефицитом вольфрама началась ее повсеместная замена на более современную сталь марки Р6М5.
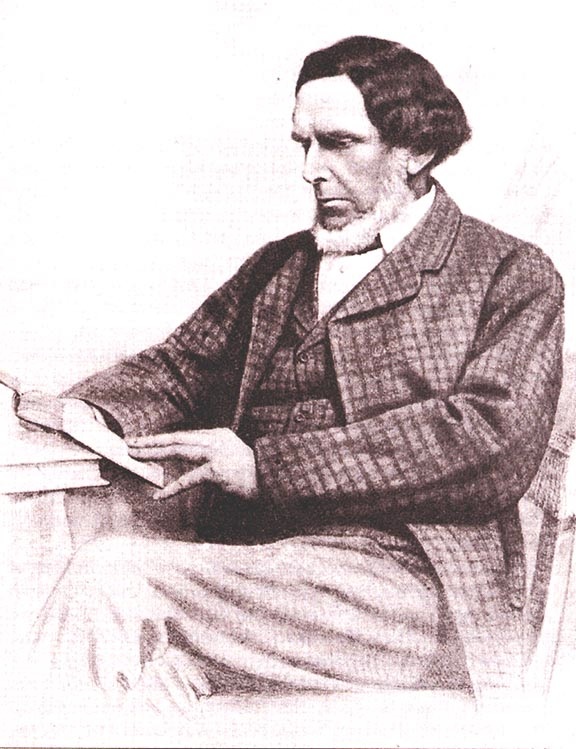
Источник фото: https://sites.google.com/site/keithlloydwebb/forest-of-dean-articles-1/father-of-steel
Главным отличием быстрорежущих сталей от традиционных углеродистых, является большое количество легирующих добавок. Именно благодаря легированию, изготолвенный из них инструмент способен работать на высоких скоростях, не доступных для стандартных "углеродок". Основным качеством "быстрореза" является твердость, сохраняемая в состоянии сильного нагрева, при котором обычные инструментальные стали подвергаются отпуску и теряют свои свойства.
Быстрорежущая сталь сохраняет рабочие качества до 600 градусов по Цельсию и при этой температуре инструмент из "быстрореза" может работать длительное время, даже раскалившись до "красного каления". При стандартной температуре (не более 200 градусов) быстрорежущие стали не имеют каких-либо преимуществ перед другими инструментальными сталями. Помимо хорошего удержания температуры, "быстрорез" демонстрирует и высокую прочность необходимую для работы сверел на больших глубинах резания и для резцов на высоких скоростях подачи. Из "быстрореза" изготавливаются сверла, фрезерные пилы, механические пилы, различные резцы и т.д.
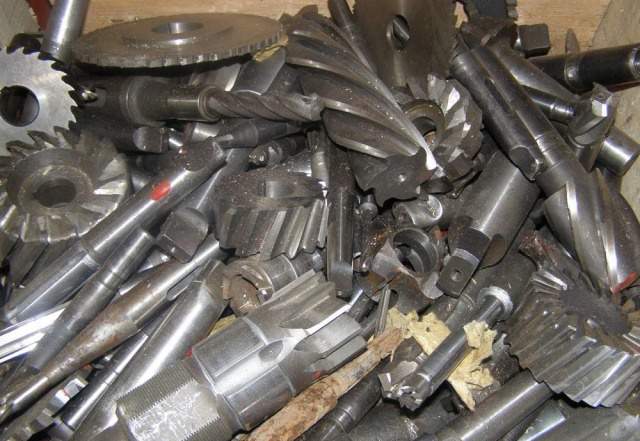
Источник фото: https://ytools.ru/62550132-Primem-Bystrorez-R18-R6M5-R9-R12-tverdosplav-vk.html
Традиционно, со времен английских металлургов, стали этой группы маркировались буквой R - «rapidsteel». В российской традиции они имеют обозначение русской Р. Первая цифра в аббревиатуре указывает на содержание вольфрама, как главного элемента быстрорежущих сталей. Кроме вольфрама, в сталях содержаться еще ванадий, молибден и кобальт, которые также на обозначаются в отечественных маркировках русскими буквами. Цифра после каждой буквы обозначает процентное содержание этого элемента в стали.
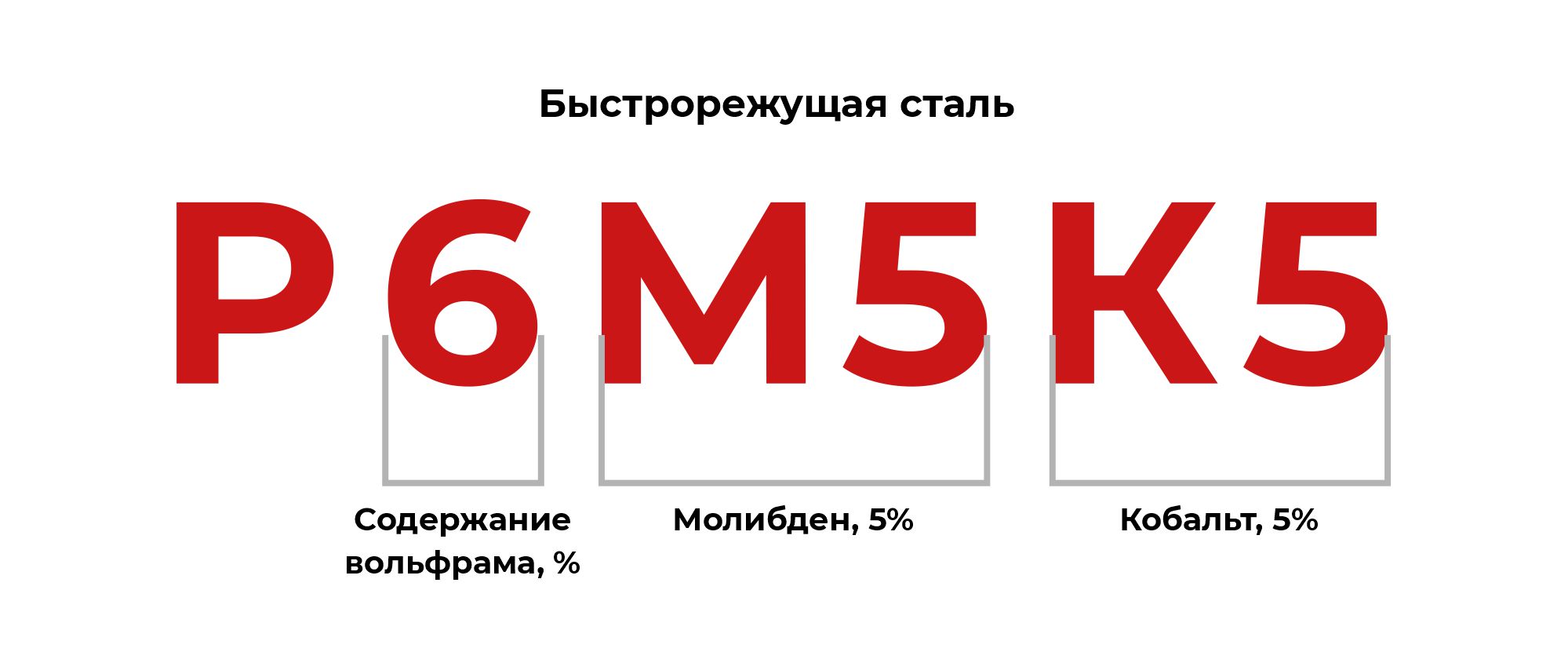
Все "быстрорезы" обладают высокой теплостойкостью, порядка 550 – 650 градусов по Цельсию. В своём составе они содержат 0,7 - 1,5 % углерода, до 18 % основного легирующего элемента – вольфрама, до 5 % хрома и молибдена, и до 10 % кобальта. В зависимости от химического состава, их подразделяют на стали нормальной и повышенной теплостойкости. Если содержание ванадия не превышает 2% - это стали нормальной теплостойкости. К ним относятся марки: Р18, Р9, Р6М5. Стали с более высоким содержанием ванадия, а также дополнительно легированные кобальтом, относят к сталям повышенной теплостойкости (Р12ФЗ, Р6М5ФЗ, Р18К5Ф2, Р9К5, Р6М5К5, Р9М4К8 и др.). Американскими аналогами российских "быстрорезов" являются стали Т11302 и М2, европейскими аналогами 1.3339, HS6-5-2, HSS, а японский аналог - SKH 51.
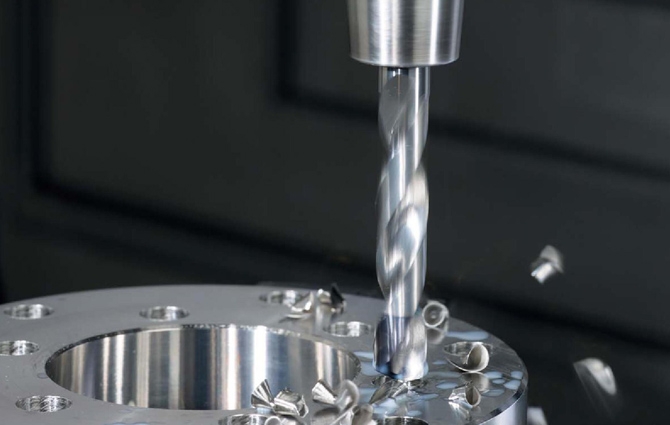
Источник фото: https://kornor.ru/blog/ugolok-pokupatelya/chto-takoe-hss-stal-vidy-i-analogi-hss.html
Термообработка быстрорежущих сталей требует особого внимания. Закалочная температура таких сталей 1200 градусов по Цельсию, калятся они с маслом, охлаждение воздушное при температуре порядка 200 градусов. Отпуск стали осуществляется при температуре 500 градусов. При этом сплавы достаточно капризны в термообработке и при ошибках быстро обезуглироживаются. Стали этой группы имеют даже свой индивидуальный дефект, возникающий при нарушениях термообработки, который приводит к повышенной хрупкости. Это так называемый «нафталиновый излом», причиной которого становится слишком высокая зернистость после закалки. Рекристализация, проходящая при очень высокой температуре может сопровождаться гигантским ростом зерна, которое потом не удается устранить. Качество быстрорежущей стали в значительной степени определяется также степенью ее прокованности. При недостаточной проковке наблюдается так называемая "карбидная ликвация", представляющая собой остатки участков ледебуритной эвтектики, не разбитых ковкой. Чем резче выражена карбидная ликвация, тем более хрупкой становиться сталь. Твердость "быстрореза" обычно порядка 65 HRC.
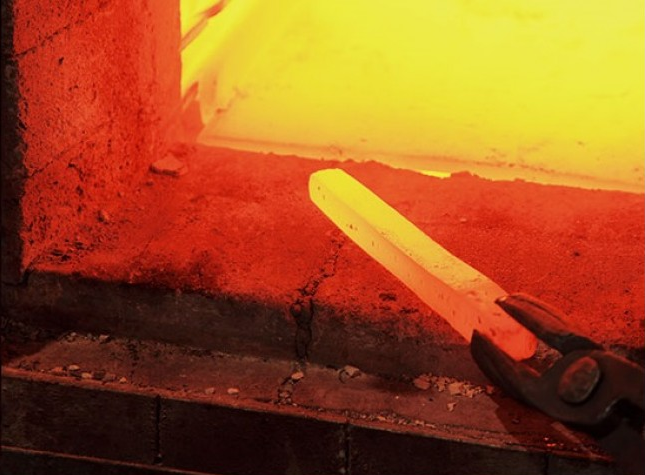
Источник фото: https://5vitkov.ru/zakalka/
Механическая обработка быстрорежущих сталей достаточно сложна. Работа с ними требует больших усилий как при ковке, так при шлифовке и полировке. При этом качество реза такими ножами традиционно очень высокое. Такие ножи сохраняют остроту достаточно долго и зачастую по показателю удержания режущей кромки оставляют стандартные углеродистые стали далеко позади. При этом необходимо помнить, что такие результаты относятся только к сравнению с «обычными углеродками»: У7, У8, У10, 65Г и т.п.
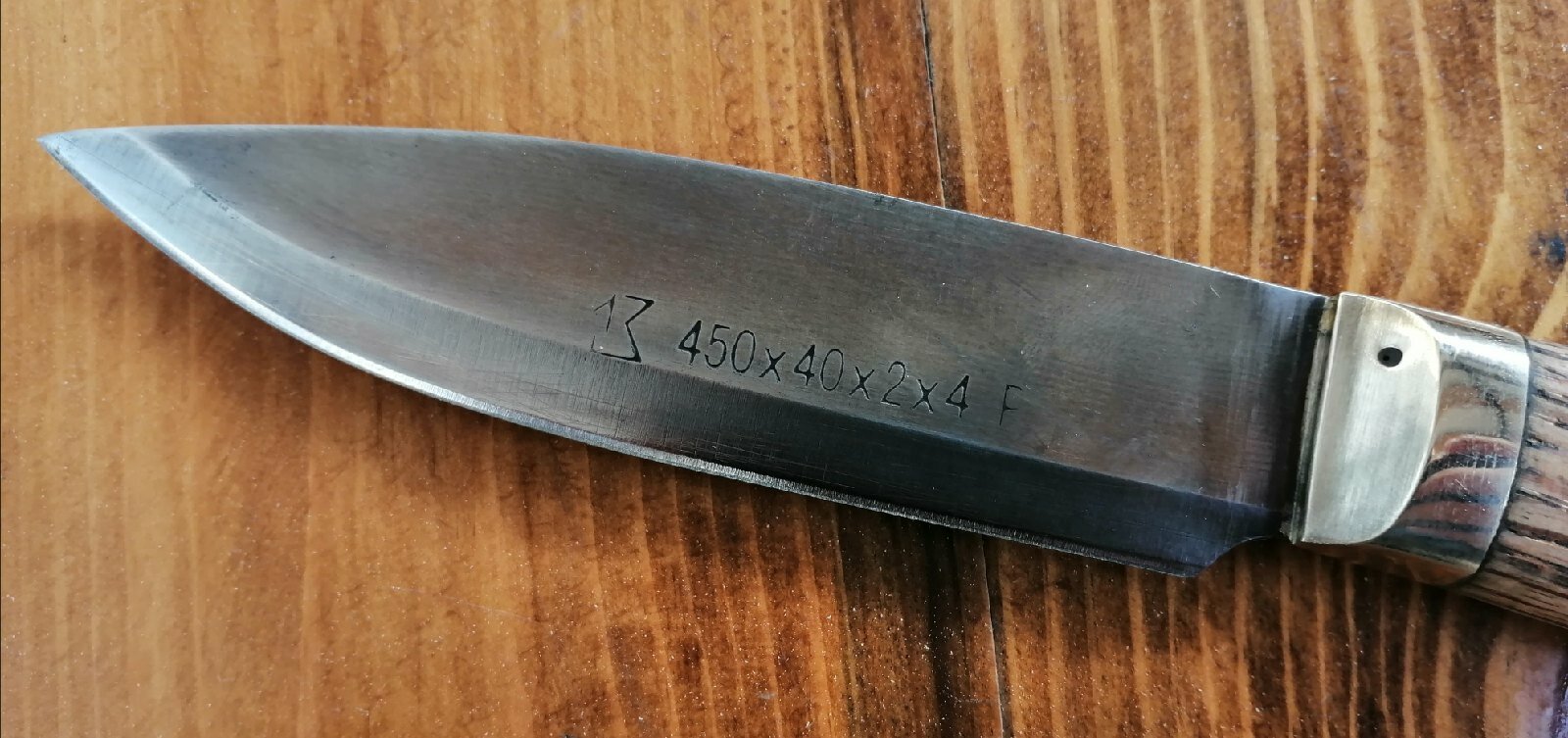
Источник фото: https://zen.yandex.ru/media/nozh_nozhny/vosstanovi-kuhonnyi-noj-iz-bystroreza-podhodit-li-stal-r6m5-...
Сравнивать "быстрорезы" с современными сталями, особенно порошковыми не корректно. Возможность легирования порошковых сталей существенно превосходит быстрорежущие, а количество углерода в них может быть больше в несколько раз. Кроме того, распределение карбидов и их размеры, сама внутренняя структура этих сталей значительно отличаются. "Быстрорезы" также не подходят для применения при ударных нагрузках и поперечных нагрузках на клинок из-за низкой прочности. Важно также помнить, что любые марки этих сталей подвержены коррозии, хотя сам процесс корродирования проходит на их поверхности несколько медленнее, чем на углеродистой стали.
Отечественная "медицинская" сталь. Уникальный материал или красивая легенда?