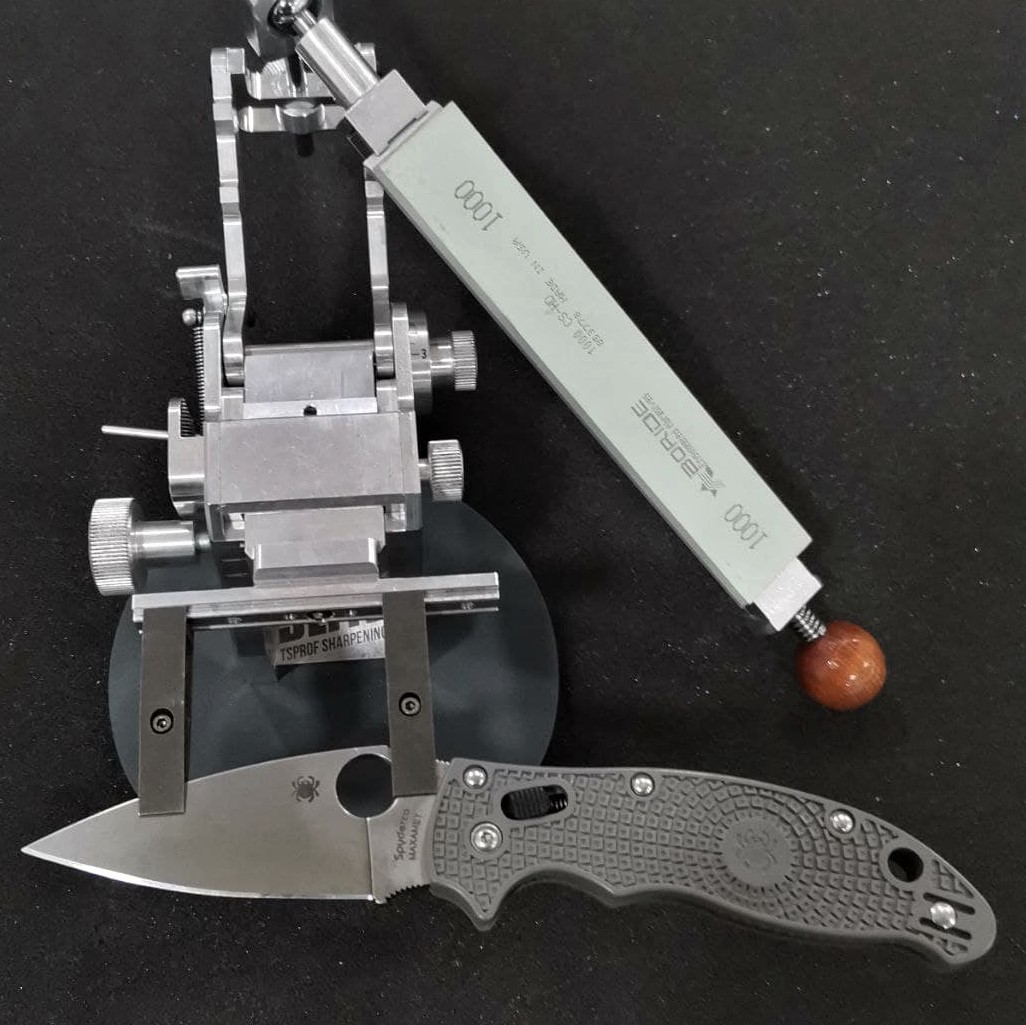
Химический состав Maxamet включает в себя 2,15% углерода, 4,75% хрома, 0,3 % марганца, 0,25% кремния, 13% вольфрама, 6% ванадия и 6% кобальта. Углерод в отвечает за твердость, износостойкость и коррозионную стойкость, но настолько высокое его количество понижает прочность на излом. Хром противодействует коррозии, однако в данном составе стали его слишком мало для того, чтобы сделать ее нержавеющей. А ключевую роль в составе играет такой компонент как ванадий, который присутствует в очень существенном количестве, максимально повышая износостойкость и ударную вязкость. Помимо этого, высокий процент вольфрама и кобальта, усиливающих твердость и жаропрочность, относит сталь в разряд инструментальных быстрорежущих. Производимые из нее инструменты могут работать на высоких скоростях при температуре до 600 градусов Цельсия.
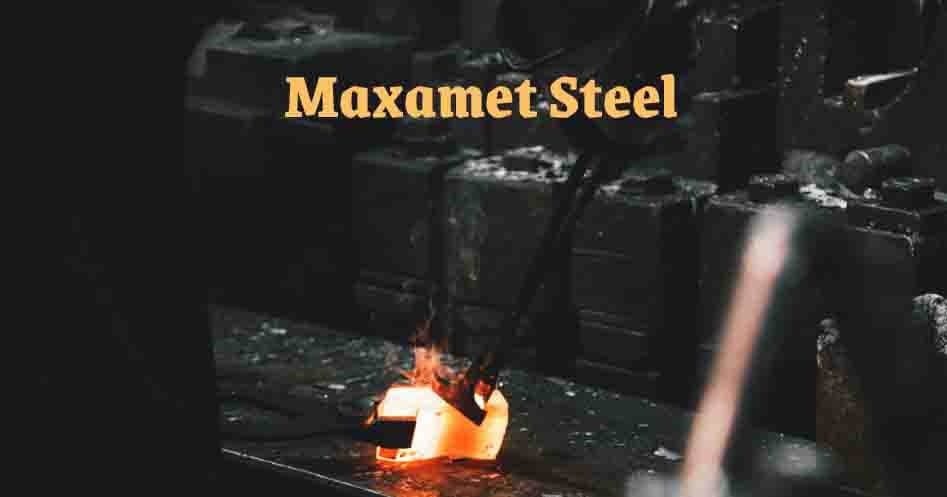
Источник фото: https://knivesngear.com/maxamet-steel-review/?__cf_chl_jschl_tk__=_2mTohlWPaOpOaQe4iziDfLUKnJFr0RsW0...
На сегодняшний день, по своим основным характеристикам, Maxamet относится к самым твердым и износостойким сталям. Ее рабочие качества максимально раскрываются при 67-68 HRC. Фактически она способна работать на предельных для ножей параметрах твердости. И имеет всего несколько конкурентов в этой нише, являясь одним из самых продвинутых и высокотехнологичных решений современной металлургии.
Износостойкость Maxamet достигается, как традиционным для «быстрорезов» легированием вольфрамом, так и применением технологии создания порошковой стали от компании Carpenter - Micro-Melt (см. статью). Именно технология порошкового передела позволяет легировать ее ванадием, причем в очень существенных объемах и сохранить при этом количество углерода более 2%. Сталь, благодаря порошковой технологии приобретает мелкодисперсную структуру карбидов, с максимально равномерным их распределением в матрице.
Источник фото: https://www.carpentertechnology.com/blog/powder-metal-alloy-bridges-the-gap
Как и любой сплав, Maxamet имеет ряд недостатков. В первую очередь - это достаточно низкая коррозионная стойкость. Небольшое количество хрома предполагает, что сталь должна ржаветь, как "стандартная «углеродка»". Однако ее уникальный состав с большим количеством ванадия, углерода и вольфрама благоприятно сказывается на стойкости. Во влажной среде сталь активно покрывается различными поверхностными пятнами и мелкими точками коррозии. Но при минимальном уходе, этот процесс не переходит в явную ржавчину и на практике Maxamet по коррозионной стойкости напоминает хорошо термобработанную сталь D2. Вторым недостатком является не очень большая прочность при боковых нагрузках. Как и любая сверхтвердая сталь Maxamet не предназначена для ударных работ по твердым материалам (рубка костей, деревьев, «батонинг» и т.п). Но в целом ее хрупкость, благодаря технологии изготовления и выдающемуся составу, не является критической. Клинок выдерживает достаточно высокие нагрузки на прочных и абразивных материалах, способен без особых проблем перерезать медные провода, пеньковые канаты, различные виды пластика. При тяжелой работе режущая кромка покрывается микросколами, но продолжает резать длительное время, не теряя агрессию.
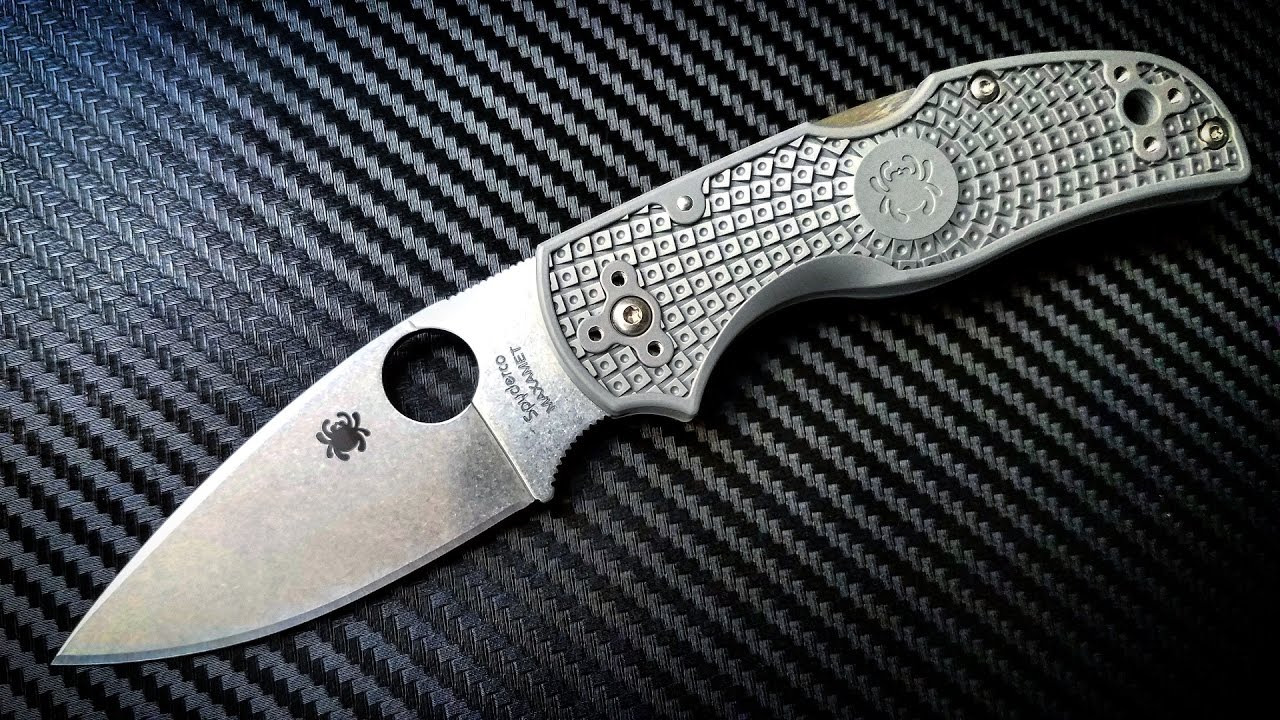
Источник фото: https://salvos.eu/ru/spyderco-native-5-micro-melt-maxamet-folding-c41pgy5/
Ближайшими конкурентами Maxamet на сегодняшний день являются «суперстали» от концерна Crucible и австро-шведской корпорации Bohler: S110V, S125V, M398, Rex 45, Rex 121 и т.п. По своим рабочим качествам все эти стали находятся приблизительно в равных условиях, подходя к пределу возможностей современных инструментальных «порошков». При этом главной чертой, объединяющей их, является слабая распространенность в современной ножевой индустрии. На сегодняшний день они используются лишь в ограниченных сериях (sprint run) крупнейших мировых брендов, либо в малосерийном производстве "кастомных" мастеров. Поэтому установить явное превосходство, как и выявить явные недостатки Maxamet в сравнении с конкурентами в массовых продуктах пока невозможно.
Заточка этого «быстрореза» требует подходящих абразивов. Заточные камни из оксида алюминия, прекрасно работающие по сталям ниже 62 HRC, не подходят для Maxamet. Им не хватает твердости зерен, а съем металла проходит крайне медленно, абразив скользит по стали. Камни на основе карбида кремния способны затачивать эту сталь, но работа ими будет медленной и потребует больших усилий. Кроме того, необходимо учитывать определённую «грубость» карбида кремния, его способность оставлять явные заточные риски, особенно на финишном этапе и микросколы на режущей кромке при небольшом угле заточки.
Оптимальным вариантом в данном случае выступают альмазные бруски, в первую очередь на органической связке и улучшенной связке OSB от Веневского алмазного завода. Они работают достаточно быстро, но в то же время мягко, не выкрашивая сталь в процессе заточки. Финишировать можно алмазной пастой того же завода на деревянном бланке, при этом будет получена зеркальная поверхность подвода.